Cuộc khủng hoảng chưa từng có tiền lệ khiến ngành ô tô toàn cầu phải thay đổi mô hình tồn tại đã 50 năm nay
Chuỗi cung ứng siêu hiệu quả mang tên "just in time" đang trải qua những biến đổi lớn nhất trong hơn 50 năm trở lại đây.
Đối với một số linh kiện, Toyota sẽ tích trữ lượng tồn kho đủ dùng trong 4 tháng. Volkswagen đang xây dựng 6 nhà máy để có thể tự sản xuất pin. Tesla thì đang cố gắng đảm bảo tốt nhất khả năng tiếp cận các vật liệu thô.
Chuỗi cung ứng siêu hiệu quả mang tên "just in time" đang trải qua những biến đổi lớn nhất trong hơn 50 năm trở lại đây. Quá trình biến đổi được thúc đẩy bởi các nhà sản xuất ô tô đang gặp rắc rối vì đại dịch. Sau một loạt sự kiện như nhu cầu biến động mạnh và thời tiết khắc nghiệt, họ đang phải đánh giá lại điều bấy lâu nay vẫn mặc nhiên đúng: bất cứ khi nào cần đến linh kiện gì, họ sẽ ngay lập tức mua được linh kiện đó.
Được Toyota giới thiệu từ cách đây hơn 50 năm, "just in time" (JIT) là mô hình sản xuất mà sẽ giữ lượng hàng hóa và nguyên liệu thô, hay chính là lượng hàng tồn kho, ở mức đủ thấp để có thể cắt giảm chi phí tối đa và tăng lợi nhuận thặng dư, đồng thời tối ưu hóa dây chuyển sản xuất.
Theo Ashwani Gupta, COO của Nissan Motor, 1 cuộc khủng hoảng chưa từng có tiền lệ như Covid đã bộc lộ rõ sự mong manh của mô hình JIT. Ví dụ như chiếc F-150 của Ford Motor, một trong những mẫu xe bán chạy nhất tại thị trường Mỹ. Phiên bản mới nhất tích hợp những công nghệ như động cơ lai giữa điện và xăng và cả phần mềm có thể được cập nhật thường xuyên như những chiếc Tesla.
Trong lúc tình hình dịch ở Mỹ đang tạm lắng xuống nhờ vaccine, khách hàng đã mua khoảng 200.000 chiếc F-150 trong quý I vừa qua, đánh dấu quý I tốt nhất trong 13 năm trở lại đây. Nhưng giờ thì nguồn cung đang bị thiếu hụt. Các nhà máy phải đóng cửa hoặc giảm công suất trong cả tháng 4 và tình trạng sẽ còn tiếp tục cho đến ít nhất là giữa tháng 5.
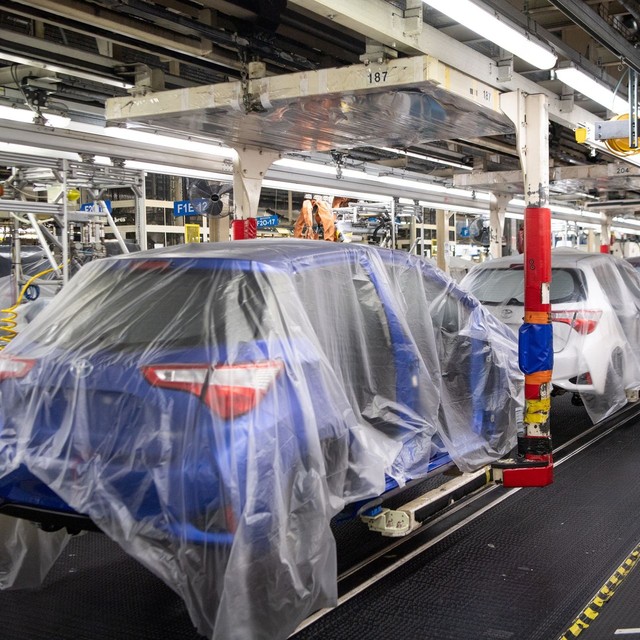
Ý tưởng cốt lõi của mô hình JIT là tránh lãng phí. Bằng cách chỉ vận chuyển linh kiện đến dây chuyền sản xuất vài ngày, thậm chí vài giờ trước khi chúng được lắp ráp, các nhà sản xuất sẽ không phải tốn chi phí cho những thứ họ không sử dụng đến, tiết kiệm chi phí kho bãi và cả chi phí nhân lực quản lý chúng.
Tuy nhiên vì mức độ toàn cầu hoá của chuỗi cung ứng ngày càng cao và các nhà sản xuất ô tô ngày càng phụ thuộc nhiều hơn vào các nhà cung ứng duy nhất, hệ thống trở nên mong manh dễ vỡ hơn và khủng hoảng xảy đến thường xuyên hơn.
Bão tuyết
Một trận bão tuyến ập đến Texas hồi giữa tháng 2 đã khiến 1 nhà máy sản xuất 85% số nhựa dẻo tổng hợp ở Mỹ phải đóng cửa. Đây là chất được dùng trong rất nhiều thứ, từ giảm xóc đến vô lăng. Dù là nguyên liệu rẻ tiền nhất trong 1 chiếc xe, đây là thứ không thể không có.
Cuối tháng 3, Toyota phải đóng cửa một số nhà máy ở Mỹ vì vấn đề này, ảnh hưởng đến những mẫu xe bán chạy nhất ví dụ như dòng xe thể thao RAV4.
Các CEO cho biết họ không muốn hoàn toàn từ bỏ mô hình JIT, bởi vì chi phí tiết kiệm được là rất lớn. Tuy nhiên họ đang dần dần cắt bỏ một số công đoạn, chủ yếu tập trung vào những phần dễ bị ảnh hưởng nhất. Các công ty tăng tích trữ những linh kiện quan trọng và gọn nhẹ như các con chip.
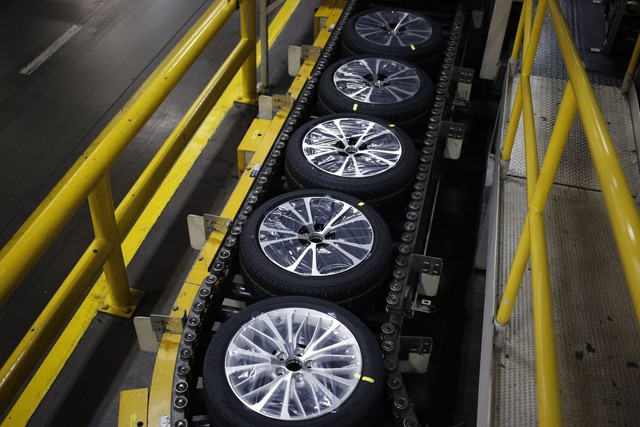
Làn sóng xe điện cũng gây thêm áp lực buộc các công ty ô tô phải suy nghĩ lại, bởi những chiếc xe điện sử dụng rất nhiều các linh kiện bị khan hiếm nhất, ví dụ như chip và pin lithium-ion. GM và đối tác LG Chem đang xây dựng 1 nhà máy trị giá 2,3 tỷ USD ở Ohio và tìm kiếm địa điểm cho nhà máy thứ 2 với mục tiêu sản xuất đủ pin cho hàng trăm nghìn chiếc xe điện mỗi năm.
Tất nhiên đảm bảo có nguồn cung pin trực tiếp sẽ không giải quyết được mọi vấn đề. Kể cả những chiếc xe điện hiện đại nhất cũng vẫn cần đến nhựa cho thảm trải sàn, cao su cho lốp xe và da bọc ghế. Tuy nhiên Tesla đang cố gắng xác định những vật liệu mang tính chiến lược nhất và tự mình sản xuất, công việc mà trong mô hình JIT truyền thống thuộc về các nhà cung ứng.
Nỗ lực của Tesla
Tháng 9 năm ngoái, Tesla ký thoả thuận để có thể tiếp cận mỏ lithium ở North Carolina. Năm ngoái Elon Musk cũng cho biết ông muốn trực tiếp mua nickel.
Động thái này của Tesla kéo lùi lịch sử ngành ô tô tới 100 năm, về những ngày mà dây chuyền sản xuất của Henry Ford là nguyên mẫu cho mọi thứ. Trong những năm 1920, Ford kiểm soát mọi thứ cần thiết để làm nên 1 chiếc xe ô tô. Nhà máy Rough River ở Dearborn, Mich., không chỉ sản xuất ô tô mà còn tự đúc thép từ quặng sắt được khai thác từ chính những mỏ của Ford.
Sau khi Henry Ford qua đời, công ty bán đi các lò luyện thép. Các nhà sản xuất ô tô cũng quyết định rằng tốt nhất là để khâu sản xuất thép, cao su và vận tải cho các công ty chuyên nghiệp nhất.
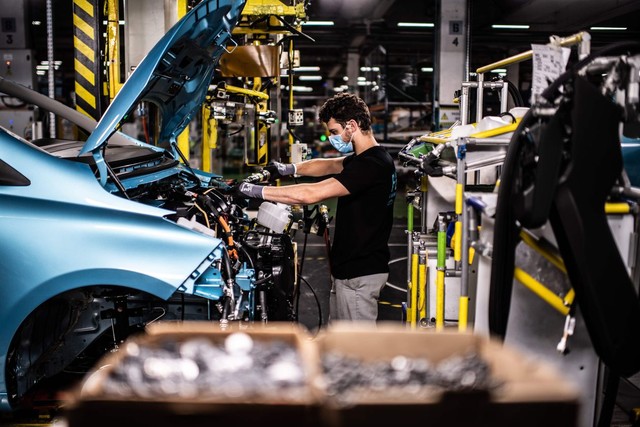
Năm 1950, CEO Taiichi Ohno tới thăm 1 siêu thị ở Mỹ và quan sát cách những kệ hàng được lấp đầy trở lại. Ông nhận thấy người đi mua sắm vẫn vui vẻ kể cả khi siêu thị chỉ có 1 kho chứa hàng rất nhỏ. Điều này đối lập hoàn toàn so với ngành ô tô, nơi các nhà kho chất đầy những tấm thép và lốp xe để đảm bảo dây chuyền không bao giờ phải ngừng hoạt động.
Thực ra thì các siêu thị có rất ít lựa chọn. Họ không thể tích trữ chuối trong nhiều tháng. Tuy nhiên, Ohno quả quyết cách làm như vậy giúp giảm đáng kể chi phí và tránh lãng phí. Toyota chỉ cần trả tiền cho những gì đủ để sản xuất ra những chiếc xe trong 1 ngày. Nhà máy và nhà kho sẽ nhỏ hơn.
Toyota có thể dễ dàng cắt giảm nhờ mạng lưới các nhà cung ứng trung thành. Ban đầu các đối thủ Mỹ không tin vào cách làm này, nhưng JIT tỏ ra hiệu quả đến nỗi tất cả các nhà sản xuất ở khắp nơi từ Detroit đến Wolfburg đều chỉnh sửa cho phù hợp và áp dụng.
Ý tưởng còn lan sang cả các ngành khác. Apple, McDonald’s và Target đều sử dụng những dạng thức khác nhau của JIT để giữ hàng tồn kho ở mức thấp.
Những sự kiện như vụ khủng bố 11/9 đã từng làm hệ thống chao đảo, nhưng ngành ô tô đều vượt qua được và tiếp tục tuân theo JIT vì phần thưởng dành cho họ quá lớn.
Gió bắt đầu đổi chiều sau khủng hoảng tài chính toàn cầu. Ít nhất 50 nhà cung ứng đã phá sản và khiến các công ty ô tô trở tay không kịp. 1 cú sốc khác là thảm hoạ động đất ở Nhật Bản năm 2011.
Bản thân Toyota đã có những điều chỉnh để mô hình JIT hoạt động hiệu quả hơn. Hãng đã xây dựng cơ sở dữ liệu về chuỗi cung ứng cho khoảng 6.800 linh kiện, đem đến cho tập đoàn khả năng phát hiện ở đâu có sự thiếu hụt và thách thức nằm ở đâu. Các công ty ô tô khác cũng đang học tập cách làm này.
"Hết lần này đến lần khác, thứ khiến chúng ta ngã quỵ không phải là những linh kiện đắt đỏ nhất mà chính là những chi tiết nhỏ bé đã không được quan tâm đầy đủ", Bindiya Vakil, CEO của nhà sản xuất phần mềm Resilinc, công ty giúp các nhà sản xuất quản lý chuỗi cung ứng nói.
Tham khảo Wall Street Journal
Thu Hương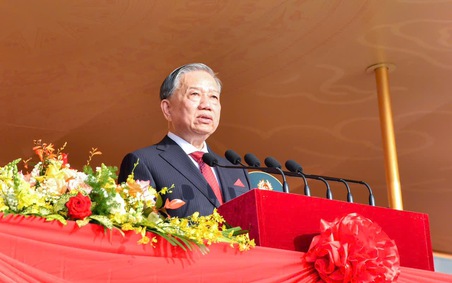
Kính thưa các đồng chí Lãnh đạo, Nguyên lãnh đạo Đảng, Nhà nước, Mặt trận Tổ quốc Việt Nam; các đồng chí lão thành cách mạng; các Mẹ Việt Nam anh hùng, Anh hùng Lực lượng vũ trang Nhân dân, Anh hùng Lao động; các tướng lĩnh, sĩ quan, chiến sĩ các Lực lượng vũ trang Nhân dân,